Magnetic separation technology
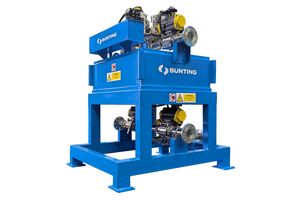
BMRA service member, Bunting, has developed a new Electromagnetic Wet Filter with an ultra-high-intensity, background magnetic field (from 3,500 up to 10,000 Gauss). The magnetic separation technology separates fine iron and paramagnetic minerals from liquids and slurries and is used in the ceramics, mineral processing, and recycling industries, as well as cleaning wastewater in steel production and power stations.
The high-intensity magnetic field of the Electromagnetic Wet Filter enables the separation of very weakly magnetic particles untouched by other magnetic separation technology. In the ceramics industry, the Electromagnetic Wet Filter removes problematic magnetic particles, both free iron and magnetic minerals, from slips and glazes. In mineral processing, more powerful Electromagnetic Wet Filters remove fine grinding iron and some paramagnetic minerals (e.g. hematite) found in non-metallic minerals. Electromagnetic Wet Filters are also used to remove free iron and scale from water in power stations, steelworks and water recycling plants.
The Electromagnetic Wet Filter provides one of the most effective methods of continually removing problematic fine iron and paramagnetic minerals from ceramic slips and glazes, as well as industrial mineral slurries (e.g. kaolin, calcium carbonate, silica sand and feldspar). The technology produces a higher separation efficiency than permanent magnetic and smaller electromagnetic separators by generating a significant background magnetic field strength in the canister (2,500 Gauss, 5,000 Gauss or 10,000 Gauss) and high magnetic field gradient on the matrix surface. The enhancement of the magnetic field on the matrix surface is between 2 and 3 times the background field – e.g. a 5,000 Gauss background filed will generate between 10,000 and 15,000 Gauss on the matrix.
An Electromagnetic Wet Filters consists of an electromagnetic coil positioned around a central hollow core containing a magnetic (400 series) stainless-steel matrix of various designs. The highly-efficient computer designed coil generates a high intensity magnetic field that becomes intensified on the points of the matrix creating the magnetic force needed to separate paramagnetic particles from the slurry.
The magnetic coil is either enclosed in a circular or rectangular steel casing designed to intensify the magnetic field into the hollow centre of the coil. The design of the oil-cooled electromagnetic coils maintains thermal stability whilst generating high Gauss values. The coil designs are energy efficient and maintain low operating temperatures.
Valves trees (for the product feed and exit as well as cleaning water and air) are mounted on the top and bottom to suit the application and installation.
Removal of the captured magnetics inside the Electromagnetic Wet Filter is either undertaken manually or automatically. For fully automated operation, the Electromagnetic Wet Filter and process is managed through a separate control. The control has a Siemens S7-1200 PLC incorporating Siemens HMI. Via the control, operators are able to set the frequency and parameters of the matrix cleaning regime.
The directional flushing system ensures the maximum removal of captured magnetics and para magnetics from the matrix, maximizing magnetic separation from the next batch of product.
The Electromagnetic Wet Filter is fitted with a built-in jig to enable easy removal of the matrix, poles, and complete canister for maintenance and additional cleaning. The jig keeps production downtime to a minimum, whilst making matrix handling safer and easier. A separate transformer rectifier is used to deliver power.
“The new Electromagnetic Wet Filter solves a high-intensity magnetic separation problem for liquids and slurries,” explained Adrian Coleman, Bunting’s European Technical Director. “In ceramics, successfully removing any magnetic particle significantly reduces reject rates and rework costs. Having the ability to process non-metallic minerals in a wet state saves on drying costs and enables higher removal levels of magnetics. The new Electromagnetic Wet Filter answers many wet magnetic separation questions.”