Provided by BMRA service member, UNTHA
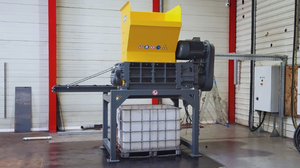
Precision cleaning specialist Proficio has advanced its metal processing capabilities, with the move to a new 20,000 sqft building in Lanarkshire, and the strategic investment in an UNTHA RS50 from BMRA service member, UNTHA.
With long-standing experience in the decontamination of metal turnings and superalloys, the team already had a comprehensive wash-line. With customers all over the world, Proficio uses progressive chemistry to clean, dry, package, and return these crushed materials for global remanufacturing.
But the expansion of the business and the procurement of a four-shaft metal shredder, means Proficio can now process uncrushed swarf by shredding the metal turnings on-site. Known for particle precision and its ability to handle difficult materials, the UNTHA RS50 shreds and reshreds the material in a single pass, with an in-built and interchangeable screen regulating the output material size.
Currently handling 1,100-1,700kg of metal per hour, Proficio shreds down to a 20mm chip, optimal for efficient downstream cleaning and maximum shipping density.
By extending the service range and eliminating a step in the process, for the customer, Proficio could double the size of its operation over the next three years.
Commenting on the decision to invest, Proficio’s managing director Mark Semple said: “Metal cleaning sounds quite simple in theory, but in practice our business is extremely complex. Throughputs are critical, so finding a resilient machine – capable of withstanding the pressures of metal shredding – was our priority.
“Increasing our in-house processing capabilities by investing in our own shredder was a leap of faith. However, we have definitely made the right decision.”
Mark conducted thorough market research and due diligence before even contacting UNTHA.
“I spoke to a number of customers and peers regarding their own shredding experience, and the feedback was always that UNTHA is the best,” he elaborated. “Site visits and a visual inspection of the material showed the consistent quality of the chip, and the knowledgeable dialogue when I eventually contacted UNTHA, cemented my decision.”
Comprehensive user training was provided by UNTHA as soon as the RS50 had been commissioned. A maintenance and cleaning regime – integral to Proficio’s operations – was also defined, as well as a fully-supported, two-year UNTHA service plan.